Table of Contents
Having an effective warehouse barcode system is essential to any business such as a dsitrbution center, which sees a high volume of goods and productsmoving around, entering and leaving the facility.
Because a warehouse barcode system helps to keep track of the volume and location of inventory, in turn allowing workers to undertake their jobs in the most efficient way possible.
A key piece of equipment for those workers is a warehouse barcode scanner, which will be used to process large amounts of information contained within barcodes, incluiding the likes of handling instructions, as well as the details of a product’s weight and dimensions.
Having a well-designed warehouse barcoding system in place that is used by operatives properly equipped and trained to use it will not only increase speed and efficiency, but will also help reduce errors and minimize opportunities for human error.
Contact us if you are looking for a supplier of warehouse labels in Brazil, Mexico, or the United States.
6 top tips for implementing a warehouse barcode system
If you are looking to implement an efficient warehouse barcode system, the following tips are worth taking into consideration.
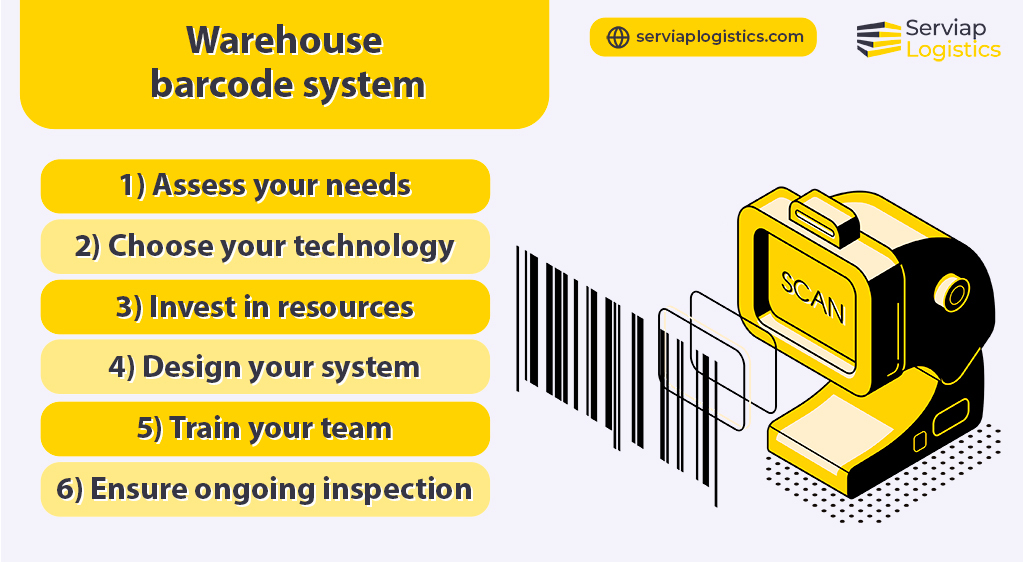
1) Assess your warehouse needs
Before diving into the implementation process, it’s essential to assess your needs and objectives. Consider what types of products you handle, and how frequently they move. It’s vital to know how many employees will be using the warehouse barcode system and what will be your budget for software and equipment.
Make a list of all existing variants for the warehouse. This stage may also involve a review your warehouse layout design, to make sure that your warehouse barcode system fits with other aspects of the layout and workflow of the facility. This will help you decide where to place barcodes and what systems to use. Remember that every item should have a unique barcode number and storage location assigned, and a process should be in place to review and scan items.
2) Choose the right label technology
There are various barcode technologies available, each with its own set of advantages. The most common and cost-effective type is the traditional 1D barcode, made up of vertical black lines. Another option is the 2D barcode, which can store more information, with black and white squares or dots. 1D barcodes are commonly seen in retail products, while 2D are used in the likes of QR codes and MaxiCodes, and have become increasingly common in recent years.
If you want more advanced labels, you can also invest in radio-frequency identification (RFID) tags, which use radio waves to transmit real-time data. They are the fastest option for daily accuracy but are usually more expensive. So, in the end, your choice will depend on which technology aligns best with your warehouse’s needs and budget constraints.
3) Invest in hardware and software
To implement a warehouse barcode system succesfully, you’ll need hardware and software components to read data from labels. First, you need inventory and asset management platforms, such as Warehouse Management Systems (WMS). Choose a software that integrates seamlessly with your barcode system. This software will help you track inventory, manage orders, and optimize warehouse operations.
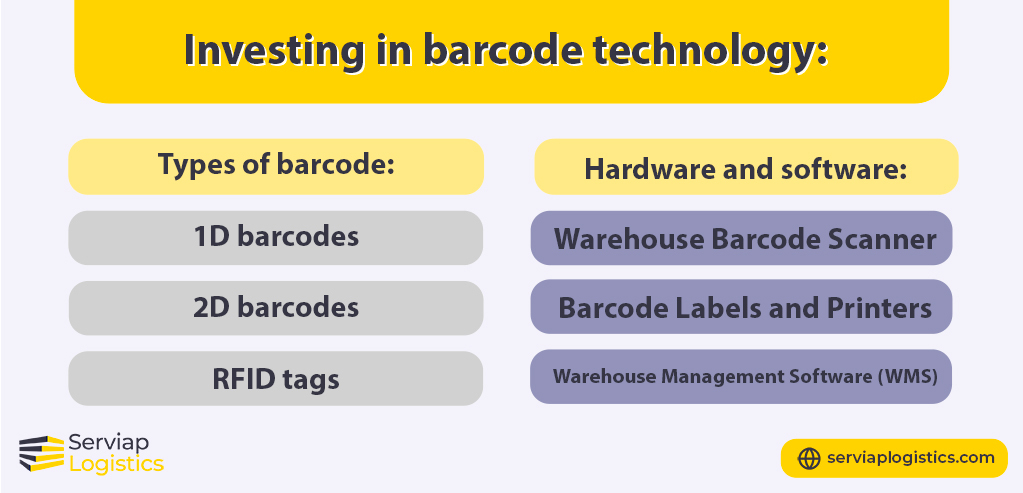
Other than that, hardware options include devices such as label printers and, most importantly, warehouse barcode scanners. These handheld devices are used to scan barcodes anywhere they are placed. There are many models, and they can be integrated, online or offline. The best choice will depend on your physical and inventory needs, so focus on flexible and ergonomic options.
4) Design your barcode system
Next, you can design a barcode system that suits your warehouse layout and inventory management processes, merging your label choices, software, and hardware. At this point, you must consider the aspects such as label placement, label format, and data fields. Carefully designing your warehouse barcode system is what will give your staff the most effective real-time view of the whole facility.
Decide where to place labels for easy scanning. Then, define a format for your barcode labels, ensuring they contain all necessary information, and that you follow an integrated standard throughout the whole facility. In this process, determine the data fields you want to include in your barcodes, such as product IDs, descriptions, or quantities, according to the software you’ll use.
5) Train your team thoroughly
Once your warehouse barcode system is ready to go, it’s time to train your team and make sure all workers are able to understand the methodology easily. It’s important to test your system before use not only to instruct staff, but also to fine-tune its performance, collect data, and make adjustments as needed to optimize efficiency further.
Ensure that your employees understand how to use barcode scanners, locate and scan barcodes accurately, and troubleshoot any issues that may arise. Ongoing training and support are essential to maximize the benefits of the system. Barcodes are customizable for every warehouse, so your staff must be prepared for how the processes will work in your facility specifically.
6) Ensure ongoing inspection
Finally, when you’re assured that your warehouse barcode system is functioning properly, roll it out gradually across your operations. Continuously monitor performance, reviewing the system’s effectiveness and making improvements where necessary. As your operations scale up, you may find the need to add extra steps in the scanning process, or even simplify it for faster results.
Many times, the software companies you’ve subscribed to will offer inspection and troubleshooting services to help you solve any issues that may appear. Additionally, you might want to consult a warehouse setup consultant for expert insight on barcode equipment, hardware, and overall processing efficiency.
Common places for applying barcode labels
Combined with the right software and hardware, the placement of barcode labels can also maximize the efficiency of a warehouse barcode system. The first labels to consider are the ones that will be applied directly to the products as soon as they arrive. Individual barcode labels can be content labels, but they may also contain handling instructions that can be read via a warehouse barcode scanner.
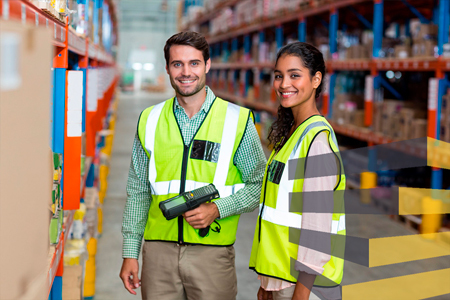
Then, barcode labels can also be applied to shelves, determining racking organization styles, number of units stored, and so on. Barcodes on shelves can be used to separate products into bigger groups as well, creating an extra step for organizing and helping staff in finding similar items. You can label racks in a standard way, or with the serpentine pattern, in a back-and-forth movement.
Furthermore, warehouse aisle signage systems will likely use barcodes to help with corridor identification, give indications, or provide easy inventory tracking. These labels are based on a numbering or sequence of characters. They are usually fixed with double-sided adhesive tags or screws at the entrance or at decisive spots in aisles.
Floors can be labeled with barcodes too, to mark inventory sitting on the ground or close to floor levels. They help reduce instances of overstocking or stockouts by being easily accessed by workers when they are transiting between corridors and aisles. New staff can quickly grasp the layout of the warehouse, thanks to the visual cues provided by warehouse floor labels.
The benefits of implementing a warehouse barcode system
Establishing a warehouse barcode system can provide several benefits that improve operations, especially as the warehouse barcode scanner market is growing fast thanks to the digitalization of distribution centers, according to FMI. Barcodes tend to be more straightforward and cost-effective than other tracking methods.
After integration, an efficient warehouse barcode system reduces human error associated with manual data entry and control. Using a warehouse barcode scanner is more precise than manually typing in product codes. This way, picking and packing orders becomes faster and more automated. This means fewer mistakes in fulfilling customer orders as well.
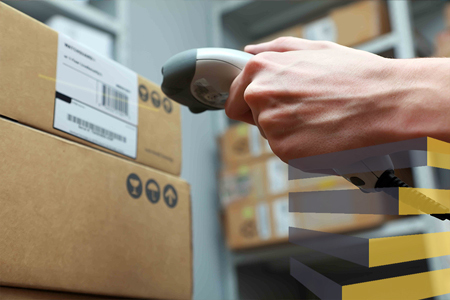
Then, as tasks are completed more effortlessly, fewer staff members may be required to manage operations, which can lead to extra cost savings. It can also help with scalability and morale, considering that workers are able to worry less about repetitive minor tracking errors. Barcodes are a great way to replace manual paperwork and physical documentation, while still ensuring compliance and regulation.
Ultimately, the barcode system helps you integrate all stages of distribution, enabling improved customer satisfaction, as people will receive the correct products in a timely manner. This can assist any kind of distribution center and is crucial for an ecommerce warehouse setup, where the fastest delivery demands are expected.
Serviap Logistics can assist you with warehouse barcoding
Serviap Logistics provides a range of warehouse setup and inventory services in Brazil, Mexico, and the United States. We can help you with optimizing your operations and creating an effective warehouse barcode system.
Our services include supplying labels, as well as providing and installing warehouse racking, collision barriers, floor marking, and signage.
Our clients include some of the biggest and best-known companies in the world from a wide array of industries, including agriculture, automotive, e-commerce, and wholesale. They choose us as a partner because of our ability to hit tight deadlines without compromising on safety and quality.
Contact us for more information.